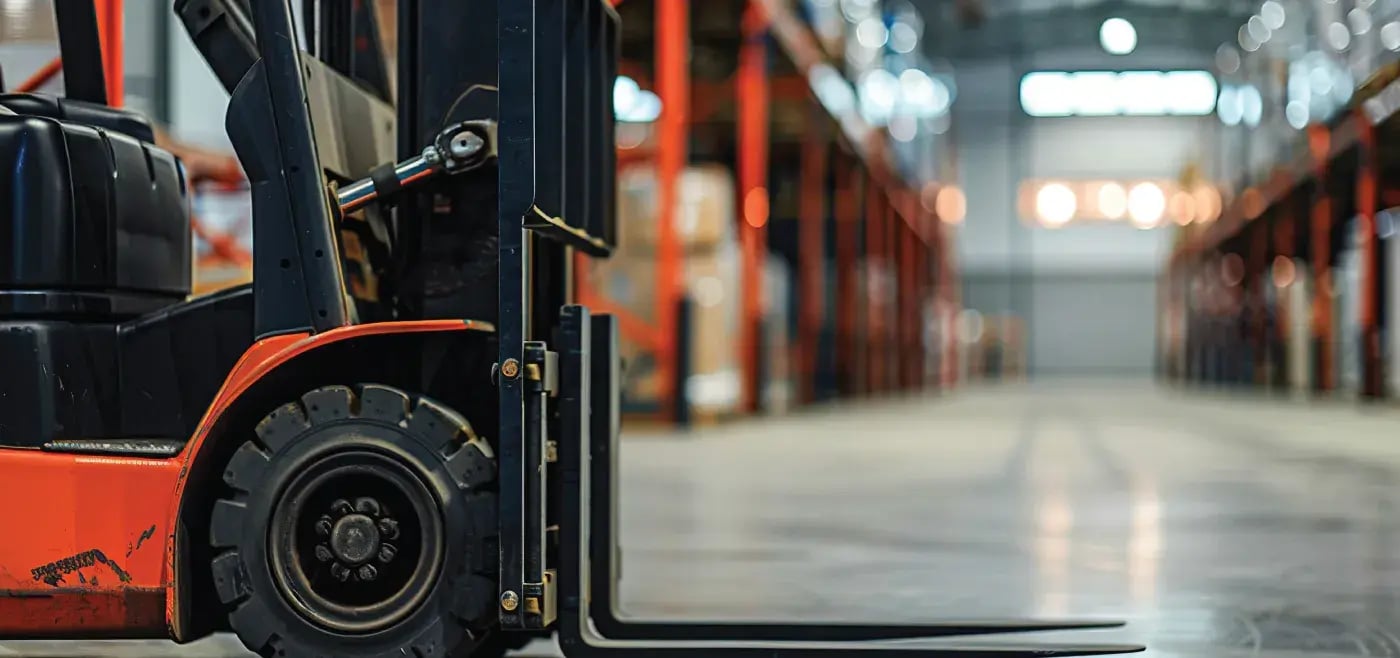
Injection Moulding for Material Handling
Strength, Durability, and Precision for Material Handling
Cost-effective, durable injection moulding for material handling
In the material handling industry, balancing durability and cost is critical. Weak components can fail under pressure, disrupt operations, and increase costs. You need reliable parts that perform every time.
PenPlast specializes in creating injection moulded products like bins, totes, and scoops, using high-volume production and commodity-grade plastics to meet your needs. With over 45 years of experience, we ensure every component delivers the strength, durability, and consistency you require.
Our RFID labeling and barcoding expertise add functionality to your products, while efficient production processes and bulk material purchasing keep costs low. Partner with us to simplify your supply chain and keep your operations running smoothly.
Let’s build something great together.
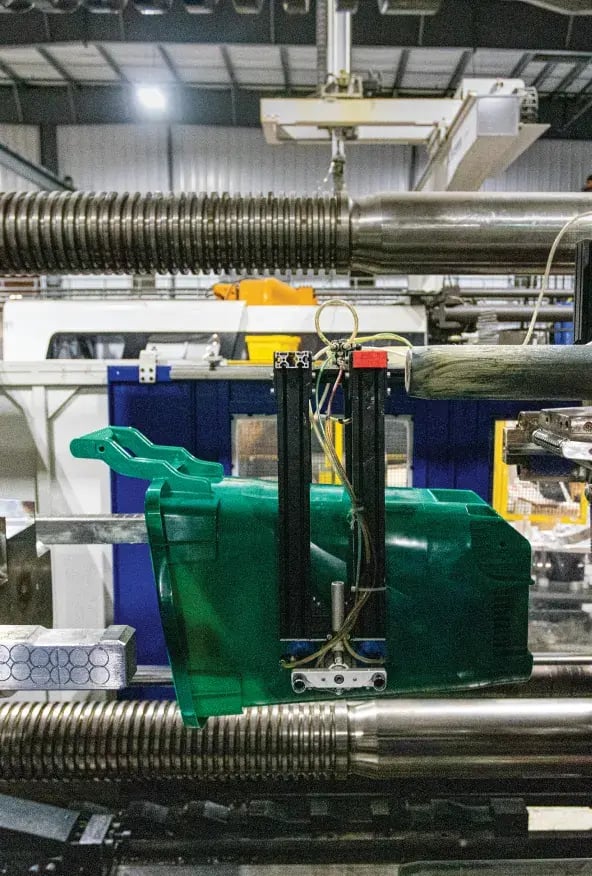
Materials engineered for strength and efficiency.
Polypropylene (PP)
A durable, versatile plastic ideal for material handling products.
- Impact Resistance: Handles drops and heavy loads without cracking.
- Lightweight: Reduces overall product weight for easier transport.
- Cost-Effective: Perfect for high-volume applications.
Polyethylene (PE)
A reliable material for heavy-duty use.
- Durability: Built to withstand demanding environments.
- Moisture Resistance: Performs well in wet or humid conditions.
- Sustainability: Available in eco-friendly, post-consumer recycled (PCR) grades.
Custom Material Options
applications
Totes & Bins.
Scoops & Funnels.
Custom RFID-Enabled Products.
Choose PenPlast. Your partner for precision moulding.
PenPlast is here to help you build stronger, more reliable systems with precision-made injection moulded components.
On-Time Delivery
Cost Savings
Unmatched Quality Control
Customizable Designs
Sustainable Practices
Your all-in-one partner for injection moulding design
Simplify your supply chain with a single partner handling every step of your injection moulding process.
- Save time
- Reduce costs
- Cut lead times
- Boost efficiency