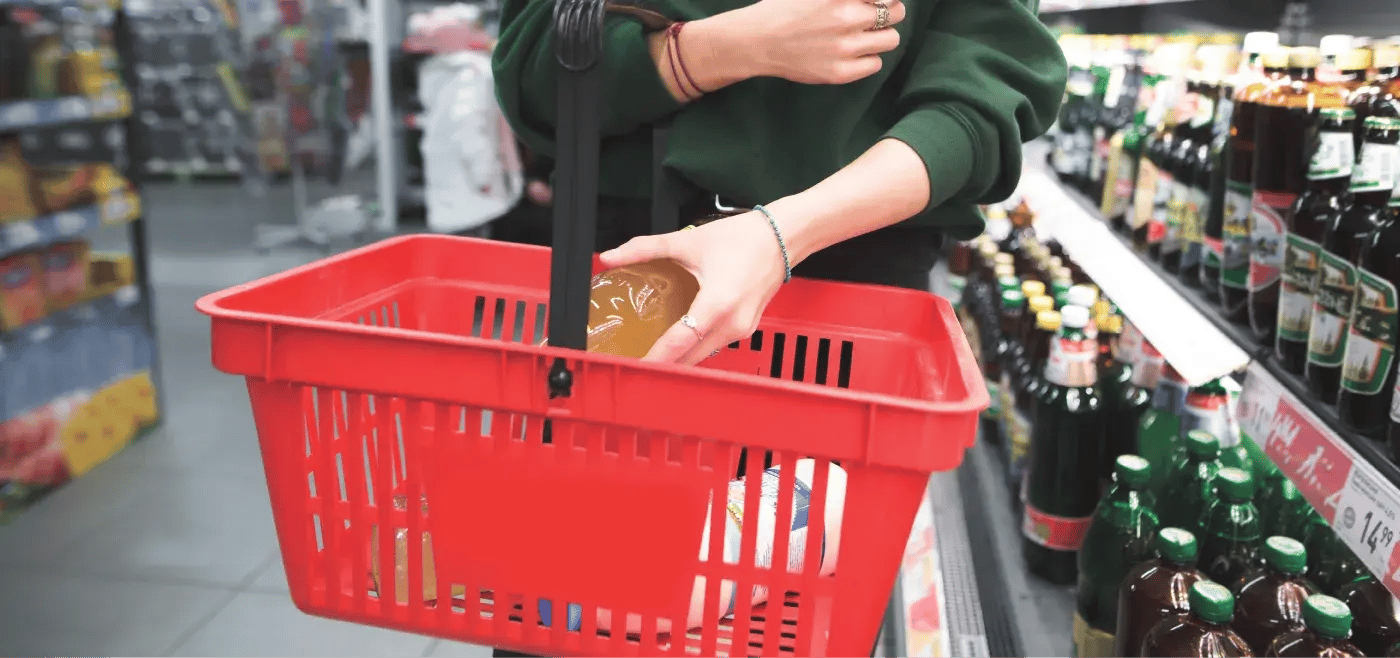
Food & Beverage
Injection moulding for Food & Beverage.
Safe, efficient, cost-effective injection moulding services for the food and beverage industry.
Meeting food safety regulations, ensuring consistent quality, and managing costs are all critical in the food and beverage industry. At PenPlast, we’ve spent over 45 years helping manufacturers like you overcome these challenges with precision-made, high-volume injection moulding.
We offer food-grade commodity plastics like polypropylene and polyethylene, certified clean production processes, and rigorous quality assurance programs. Whether you need NSF-certified serving trays or custom pails for food storage, we ensure every product is compliant, durable, and delivered on time.
When you work with us, you’ll gain a trusted partner who understands the demands of the food and beverage industry, from fast turnaround times to inventory flexibility during peak seasons.
Our Food Safety Certifications |
|
|
Let’s keep your production running smoothly.
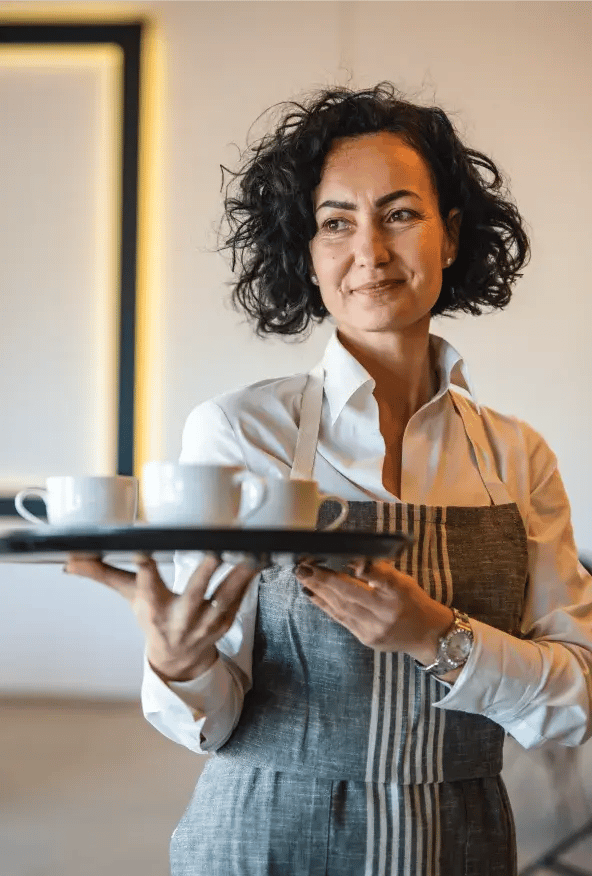
Durable, food-safe materials designed for standards.
Polypropylene (PP)
A versatile, food-grade plastic perfect for various applications.
- Durable and lightweight: Withstands wear and tear from high use.
- Chemical Resistant: Withstands common food and beverage substances.
- Moisture Resistant: Protects products in demanding environments.
- Food-Safe: Meets NSF and HASP standards for food contact.
Polyethylene (PE)
Cost-effective and reliable for bulk production.
- Durable: Perfect for heavy-duty trays and pails.
- Chemical Resistant: Handles exposure to cleaning agents and food-grade chemicals.
- Moisture Resistant: Ideal for products exposed to liquids.
- Eco-Friendly: Available in PCR grades for sustainability.
Custom Material Options
applications
Choose PenPlast. Your partner for precision moulding.
At PenPlast, we provide reliable, high-quality injection moulding services backed by decades of industry experience.
Fast Delivery
Save Money
Stay Compliant
Handle Seasonal Demands
Eco-Friendly
Your all-in-one partner for injection moulding design
Simplify your supply chain with a single partner handling every step of your injection moulding process.
- Save time
- Reduce costs
- Cut lead times
- Boost efficiency